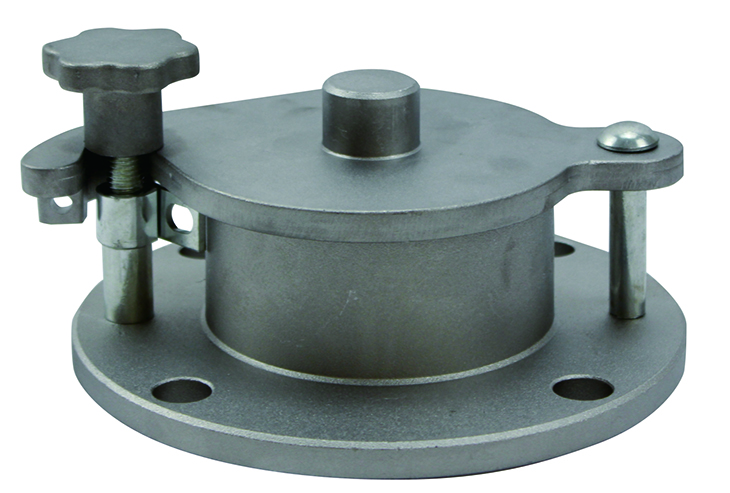
Double-sealed oil measuring hole
Use and Characteristic of Oil Filling Hole
Use:
The oil filling hole serves as a crucial measuring inlet for daily use by service station staff. It is strategically positioned on the top of the oil tank, where its flange plate connects seamlessly with a short neck flange plate located at the tank's base. This configuration ensures that the oil quantity oil hole is in direct communication with the tank's inner cavity, facilitating accurate and efficient filling operations.
Characteristic:
Dual Closure Design: The oil filling hole boasts a unique clamshell closed hole combined with a ball core sealed double closure system. This innovative design effectively prevents the leakage of oil and gas, safeguarding the environment against potential contamination.
Enhanced Security: The incorporation of a double padlock structure significantly enhances the hole's resistance against unauthorized access, prying, and external damage. This feature ensures that the oil filling hole remains secure and tamper-proof.
Flip-Open Design: The clamshell cover features a flip-open design that allows for easy access while maintaining tight seals. The locking handwheel ensures a secure closure, and the embedded oil ring within the groove prevents sparks generated by the impact of the closed cover and iron components.
Spark and Electrostatic Prevention: Recognizing the potential for sparks and static electricity during measurement, the oil hole incorporates a copper sleeve within its orifice. This design prevents sparks and electrostatic discharge, ensuring the safety of the filling process.
Copper Guide Groove: A 360-degree rotating copper guide groove (Tou Chicao) is thoughtfully designed at the fixed measuring point. This feature facilitates smooth and precise dipstick and sampling barrel operations, minimizing friction and wear.
Durable Construction: The oil hole is crafted from high-quality aluminum alloy casting material, ensuring a compact and sturdy structure free from blisters and pores. The use of nitrile rubber for the sealing ring offers exceptional oil resistance, corrosion resistance to ethanol, and aging resistance, meeting the rigorous demands of sealing oil tanks.
Environmental Compliance: With its emphasis on preventing oil and gas leakage, the oil filling hole aligns perfectly with modern environmental protection initiatives, making it an ideal choice for service stations looking to minimize their environmental footprint.
In conclusion, the oil filling hole represents a significant advancement in the design and functionality of oil measuring inlets. Its innovative features, including dual closure, enhanced security, and environmental compliance, make it a reliable and efficient solution for service stations worldwide.
The gas station's oil measuring hole incorporates several key features aimed at enhancing safety and preventing oil and gas leaks during the oil recovery process. These features include:
Clamshell Closed Hole and Ball Core Double Seal Design: This design utilizes a clamshell that closes over the hole, combined with a ball core seal, creating a double barrier that effectively prevents the leakage of oil and gas. This double-sealed system ensures a secure and environmentally responsible method of oil recovery.
Double Padlock Structure: The addition of a double padlock structure further enhances security by making it more difficult for unauthorized access or tampering. This feature deters prying and protects against artificial external damage, ensuring the integrity of the measurement process.
Flip Open Design with Sealed Cover and Locking Handwheel: The flip-open design allows for easy access to the measurement hole while maintaining a secure seal. The sealed cover and locking handwheel prevent accidental or intentional opening, and the seal itself is embedded with a groove-resistant oil ring to minimize the risk of sparks during closure. This design ensures that even if the cover is accidentally struck by metal objects, sparks are prevented.
Copper Sleeve Inside the Orifice: To address the potential for sparks and static electricity generated by the friction between the dipstick and the sampling barrel as they contact the hole, a copper sleeve is embedded inside the orifice. The copper sleeve acts as a grounding mechanism, diverting any sparks or electrostatic discharge safely away, minimizing the risk of ignition in the presence of flammable gases.
360-Degree Rotatable Copper Guide Groove (Tou Chicao): Located at the fixed measuring point, this feature allows for smooth and easy insertion of the dipstick or sampling equipment. The 360-degree rotation capability ensures that the dipstick can be aligned correctly every time, reducing friction and wear on the orifice. The copper material of the guide groove also contributes to the overall safety by further minimizing the risk of sparks during the measurement process.
The use of Aluminum Alloy as the casting material for this type of oil hole part is advantageous for several reasons. Aluminum Alloy is known for its compact and firm structure, which ensures durability and stability during use. The absence of blisters and pores in the casting further reinforces its structural integrity, preventing potential leaks or weaknesses that could compromise the part's performance.
The inclusion of a sealing ring made from nitrile rubber is a smart design choice. Nitrile rubber exhibits excellent oil resistance, meaning it can withstand prolonged exposure to various types of oils without degrading. Additionally, it is corrosion-resistant to ethanol, ensuring compatibility with fuel blends containing ethanol. Its aging resistance ensures that the sealing ring maintains its effectiveness over time, even under harsh conditions. These properties make it an ideal material for sealing oil tanks, ensuring a tight and reliable seal that meets the demands of the application.
The factory's production model for these oil holes is designed with both practicality and efficiency in mind. The reasonable design and simple structure facilitate easy installation, reducing the time and effort required for maintenance or replacement. Moreover, the oil hole's performance is not affected by external factors such as weather conditions or temperature fluctuations, ensuring reliable operation in a wide range of environments.
From a measurement management perspective, this design supports accurate and efficient monitoring of oil products. The simple structure and installation process allow for seamless integration into existing systems, enabling accurate readings and timely interventions when necessary.
Finally, the safety of storage and transportation is paramount in the oil and gas industry. The use of durable materials and a reliable sealing mechanism in these oil hole parts contributes to the overall safety of the system, reducing the risk of leaks or accidents that could harm personnel or the environment.
In summary, the Aluminum Alloy casting material, combined with the nitrile rubber sealing ring and the factory's production model, results in a robust and reliable oil hole part that meets the demands of the oil and gas industry in terms of durability, sealing performance, installation simplicity, and safety.
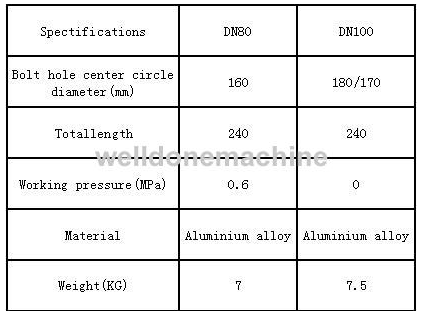